How inventory moves across locations
Introduction
Inventory movement across several locations or warehouses can be a crucial part of any business. Understanding how this information is used and where to see it is critical to anyone who needs to make decisions about anything from when to reorder or manufacture stock or when important orders are full and can be shipped. Let's take a look at how Paragon moves and tracks inventory.
Product history
In the following workflow, the product below will be used as an example. Note that products must be in an active status to be added to transactions.
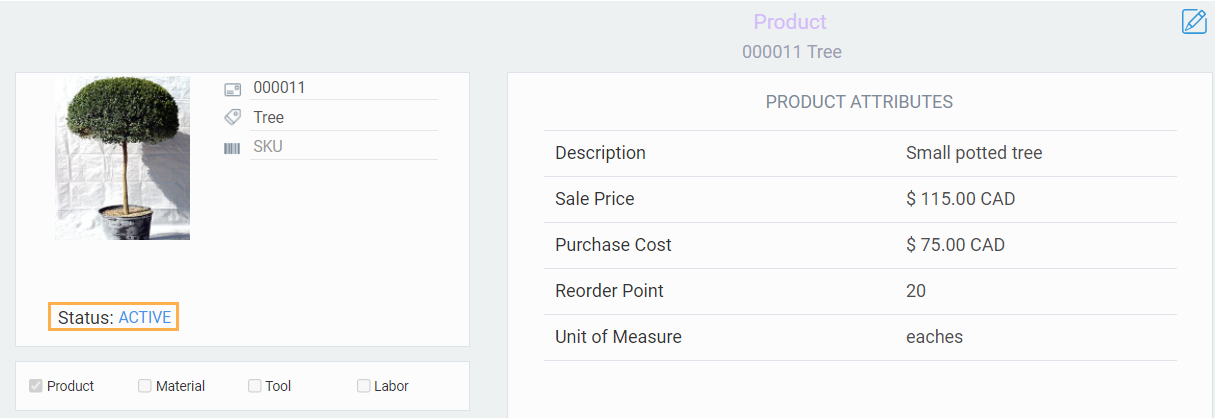
This is the history tab of the product, found in the inventory module. As you can see, there are 0 units in inventory with no inventory movement in its history.

After each transaction is created, this screen will show how the inventory was adjusted or moved through the different locations set up in Paragon.
Receipts affect inventory
Creating, issuing, and completing a receipt in Paragon will affect inventory levels. When this is done, products are received into a receiving area, which can also be renamed depending on your business modal and terminology.
In this example, we created a receipt for the product. Once the receipt was completed, the inventory was updated.
The history tab of the product shows that the inventory increased by 20 units in the receiving area.

- The net effect on the inventory is +20 units.
- Receiving Area: +20
- Net Change: +20
Transferring inventory
Now that 20 units have been received, they should be moved out of the receiving area and onto a shelf where they will be stored.
Go to the move tab of the product in the inventory module. In this example, the 20 units that were received were moved out of the receiving area into the shelving area of the warehouse.

This movement decreased the inventory in the receiving area by 20 units and increased the inventory in the shelving area by 20 units.

- The net effect of my inventory is 0.
- Receiving Area: -20
- Shelves: +20
- Net Change: 0
Picking tickets
Creating, issuing, and completing a picking ticket will also affect inventory. In the example below, we created and completed a pick ticket for the product.
This picking ticket deducted 5 units from the shelving area and added 5 units to the packing area. Creating a picking ticket moves inventory to a packing area because, in a standard workflow, the goods will be packed at the next step.

- The net effect on the inventory is 0.
- Shelves: -5
- Packing Area: +5
- Net Change: 0
Packing slips
Next, a packing slip was created from the picking ticket for 5 units. Once the packing slip is completed, the inventory will be moved again. The inventory now moves from the packing area to the shipping area, because the next step in a standard workflow is to ship out the packed box.
5 units were deducted from the packing area and 5 units were added to the shipping area.
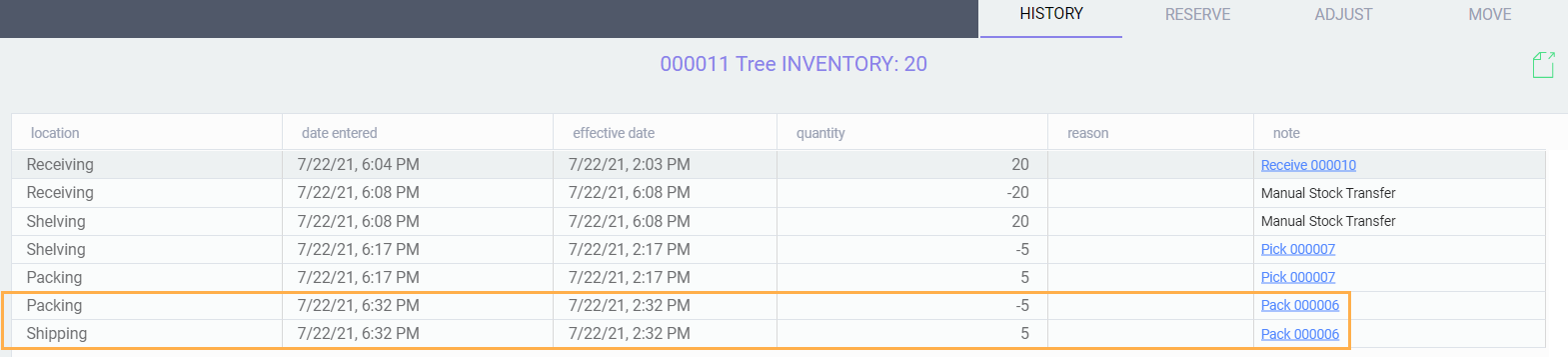
- The net effect on the inventory is 0.
- Packing Area: -5
- Shipping Area: +5
- Net Change: 0
Shipments
Next, a shipment was created off the pack list. Once the shipment is complete, inventory is updated. Completing the shipment deducts inventory from the shipping area.
The overall effect on the inventory is -5 because in reality, the goods have left your possession once they've been shipped.
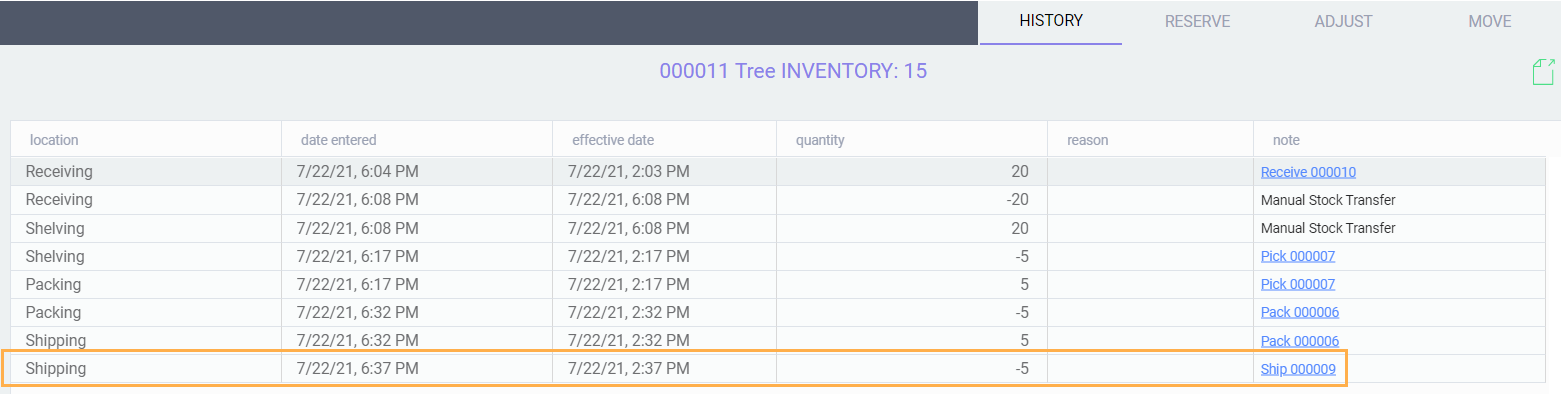
- Shipping Area: -5
- Net Change: -5
Then a pick was created and once a pick was completed, the products moved from the shelving area into a packing area.
Once the pack list is completed, the products are moved out of the packing area and into the shipping area.
Then, once the shipment was completed, inventory was deducted from the shipping area and removed from inventory completely.
Completing receipts and shipments in Paragon are the only two transactions that have a net positive or net negative effect on inventory. The other transactions simply move inventory from one area to another, with a zero net effect.
If you should decide to create a default warehouse for all transactions, it is not recommended that you activate any other warehouse locations. Doing so would adversely affect the way inventory moves across locations after completing transactions. You can either create one type of each location required for your business (default for packing, shipping, receiving, etc.), or have one default location for all transactions.
What's next?